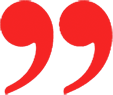
Aluminum producers face continuous pressure to keep pace with growing demand. However, achieving higher throughput while lowering emissions is a serious challenge. This case study details how Custom Alloy Sales Inc., the only combined recycled aluminum smelter and zinc alloy supplier on the West Coast leveraged Messer’s new OXIPYR® LEAF air-oxy fuel technology to further boost output while reducing emissions.
The Challenge: Increase Aluminum Furnace Throughput with Decarbonization
Based in California, Custom Alloy has successfully met the state’s emissions standards for decades with the help of Messer’s flatjet burners employing pure oxygen. With the state desiring even lower emissions in the future, Custom Alloy was searching for innovative ways to address this challenge, while increasing production to meet their customers’ demand.
Custom Alloy and the Messer metals team have had a long-standing partnership for over 20 years. The two teams conducted a furnace audit and evaluated options to overcome these challenges.
The Solution: OXIPYR LEAF Unlocks More Efficient Aluminum Production
Messer was developing a technology specifically designed to increase throughput and reduce NOx and carbon dioxide emissions for sidewall reverberatory and direct charge furnaces.
The new OXIPYR LEAF burner boosts melt rate on demand by adjusting air and oxygen when needed for optimal performance. This novel approach also reduces natural gas and oxygen consumption driving emissions down, giving melters more operational flexibility.
Messer introduced OXIPYR LEAF to Joseph Wetzel, Custom Alloy’s Plant Manager as a potential solution. Though it would be the first commercial installation for the technology, Mr. Wetzel knew the Messer metals team would deliver.
The Results: Higher Melt Rates, Greater Flexibility, Lower Emissions
OXIPYR LEAF burners were successfully installed and commissioned on one of Custom Alloy’s sidewell reverberatory furnaces in January 2023. Figure 1 illustrates the overall improved performance the operators observed in the first several months.
Figure 1: Melt rate (inches per hour) and specific energy consumption (Btu per pound) tracked in the OXIPYR LEAF furnace. Note: Messer and Custom Alloy began tracking operations from July 22 to establish proper baseline using the older burners, resulting in partial improvements before installation of OXIPYR LEAF.
The OXIPYR LEAF burners increased melt by over 15%. More metal could be charged in the sidewell and molten metal production rate increased while reducing natural gas consumption by 15%. In addition, through a strategic use of air injection during certain portions of the melting cycle, overall oxygen consumption decreased by 25-30%.
Custom Alloy and other aluminum recyclers closely monitor the amount of dross formed and metal recovery. These figures did not materially change after the installation of LEAF. Because the new control system offers the operators more furnace related data and temperature monitoring, operators have been able to improve fluxing and metal loss tracking. Thermiting dross has been reduced.
LEAF burners have achieved over 15% in CO2 emissions reduction and significantly lowered NOx emissions compared to the flatjet burners. Official results of emissions will be available as soon as California Energy Commission publishes them.
With a relationship built on trust and innovation, Messer and Custom Alloy will continue their pursuit of improved aluminum production together.
Learn more about Messer's OXIPYR low-emission burners here.
Article published originally in Light Metal Age, August 2024.
OXIPYR® is a registered trademark of Messer Industries USA, Inc