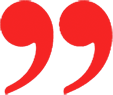
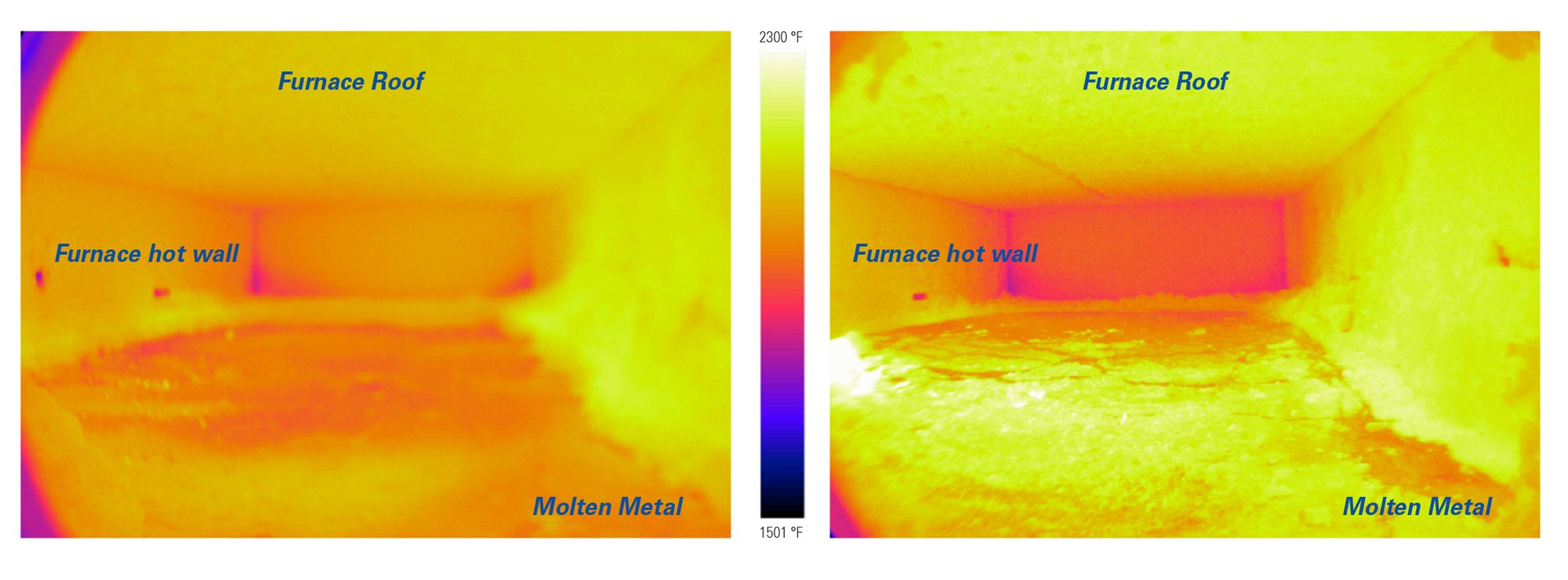
The temperature profiles of the old (left) and new (right) burners show lower refractory temperatures and a more uniform flame with fewer hotspots in the new furnace. In addition, the lower bath surface temperatures result in a reduction in dross formation.
As a leading supplier of secondary specification aluminum alloys, Bermco Aluminum is an ISO 9001:2015 certified producer of molten aluminum and cast alloyed aluminum metal products for the automotive industry. Based in Birmingham, AL, the company has been responding to the aluminum industry’s unprecedented growth in automotive by investing in state-of-the-art equipment in order to rapidly automate and upgrade its processes. This includes the installation of custom 3D-printed burners designed to improve furnace efficiency.
Oxy Fuel Combustion Development Process
for Aluminum Melting
In July 2021, Bermco approached Messer, their industrial gas and technology supplier for the last 25 years, to help them improve furnace production capacity. The aluminum company had already been benefiting from Messer’s OXIPYR® flat jet burners using oxy fuel for many years.
During oxy fuel combustion, fuels combust with pure oxygen to improve furnace throughput and reduce carbon dioxide and nitrogen oxide emissions. While this method has worked well for Bermco, the company wanted to further improve the performance of its furnaces.
“We wanted to increase the throughput and refractory life of our two side well reverberatory furnaces,” said Tim Goff, plant manager for Bermco Aluminum. “We were looking for quick, low capital improvements that could increase production without adding labor.”
Messer’s team was well positioned to respond to Bermco’s needs, as the company’s team had been exploring ways to reduce fabrication costs on custom-designed OXIPYR burners through the use of 3D metal powder printing. When using conventional fabrication techniques, optimizing burner design for a particular furnace was not economical. However, with the advancement of 3D printing technology, those costs have been significantly reduced.
The Messer team strongly believed that installing a tailor-made 3D-printed burner would enable Bermco to increase fire rate without overpowering the refractory or their capital projects budget.
“This was an innovative solution,” noted Goff. “We could swap out the existing burners with very little downtime and improve capacity immediately.”
New Oxy Fuel Burner Design for the Side Well Reverberatory Furnaces
Messer’s combustion team conducted a detailed two-week furnace evaluation of each stage of the melting process. They verified the theoretical consumption and furnace melt efficiency calculations using thermal imaging analysis and measurements from specific locations in the furnace.
The development team used a computational fluid dynamics (CFD) model to optimize the design of the 3D-printed burners. The final burner design incorporated features that both improve the flame profile and extend the life of the refractory while increasing fire rates.
Higher Aluminum Melt Rates, Reduced Dross Formation, and Increased Refractory Life
The redesigned 3D-printed OXIPYR burners were installed in only three months after the furnace audit. The installation team used thermal imaging analysis to further validate the design and demonstrate the new production potential.
“The thermal imaging was an important step to confirm the capabilities of the redesigned burner technology,” said Goff.
Since the installation and startup on the new, larger 3D-printed burners, Bermco has seen higher melt rates within its furnace, thus increasing production. In addition, the burners are able to maintain a lower temperature on the bath surface, which resulted in reduced dross formation. With lower refractory temperatures, the newly configured burners have also extended the refractory life, reducing maintenance requirements.
“Given the current price of aluminum and the cost per relining,” explained Goff, “even a small percentage increase in production translates to significant savings and positive impact to the bottom line.”
Want to learn more about Messer’s OXIPYR technology? Contact us today!
Article published originally in Light Metal Age, October 2022.
OXIPYR® is a registered trademark of Messer Industries USA, Inc