Dissolved air flotation (DAF) is highly effective for removing fats, oils, and grease (FOG), and total suspended solids (TSS) from wastewater, yet it is less effective for reducing biochemical oxygen demand (BOD).
In many locales, that may not matter. In others, it could result in community issues or publicly owned treatment works (POTW) surcharges.
The BOD treatment solution at Koch Foods involved a custom-designed BIOX™ oxygenation system before the DAF unit.
Who is Koch Foods?
As a poultry supplier to the fast food industry, Koch Foods LLC seeks to manage operations sustainably by adhering to regulatory requirements and guidelines, minimizing environmental impact, and playing a positive role in the community.
Koch Foods’ Morristown, Tenn., deboning facility produces more than 70 million lbs of cut wings as well as boneless chicken nuggets, tenders, and breasts every year. Situated in the hills of eastern Tennessee about 50 miles east of Knoxville, the plant operates 24 hours a day, six days a week, on three eight-hour shifts. More than 600 people are involved in the production process. The total process wastewater flow rate at the plant averages about 130,000 gal per day.
From 2007 to 2011, production rates at the poultry deboning plant increased by about 50%, boosting the mass loadings of organics in the effluent. The raw wastewater from the poultry plant contains significant quantities of BOD, TSS, and FOG.
Wastewater treatment for poultry processing operations
The on-site wastewater treatment operation begins with a fine screening system for solids. Effluent then passes through an equalization (EQ) tank with mechanical mixing and aeration, and finally into a DAF system for the final separation of organics before discharge to the POTW. The DAF system includes a polymer-assisted flocculation unit to coagulate organics prior to the air flotation tank.
Despite the increase in plant production, routine compliance sampling showed the plant’s pretreatment system performing well in 2012, with treated effluent concentrations averaging about 540 mg/L BOD5, 5 mg/L FOG, and 72 mg/L TSS. Further BOD reduction occurs as part of Morristown’s municipal wastewater treatment process prior to clean water discharge into the environment.
Reducing BOD5 and plant odor
Nonetheless, the plant wanted to minimize BOD5 concentrations above 500 mg/L to limit potential surcharges from the city. Achieving this goal would not only help Morristown reduce overall BOD abatement measures at the POTW, but it could also help Koch Foods further minimize plant odor and environmental impact in the face of burgeoning demand for its poultry products.
Koch Foods contacted Larry W. Moore, Ph.D., P.E., a professor of environmental engineering at the University of Memphis, to further investigate BOD treatment solutions. The wastewater treatment complex outside the processing plant was analyzed on behalf of the city of Morristown and the Tennessee Manufacturing Extension Program (TMEP). This analysis also reviewed other treatment options to further reduce BOD cost-effectively. TMEP does not endorse or warranty any specific method, product, process, or service. It is an industrial assistance program designed to help industries make sound decisions regarding environmental management.
The wastewater treatment process is tested by Koch Foods at regular intervals every month. In the six months leading up to the new BOD control measures in July 2013, the conventional DAF system averaged 903 mg/L BOD5, highlighting the need for greater control.
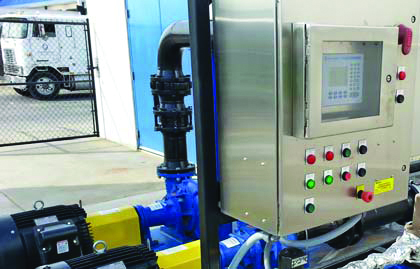
Control panel moderating appropriate oxygen flow
Options for reducing BOD in wastewater
For a baseline view of the process wastewater, seven different wastewater sources from the processing plant were analyzed to estimate their contributions of BOD5, soluble BOD5, TSS, and FOG to the overall waste stream. Although there were limitations in the sampling due to the variability of organic solids, testing revealed that the primary skinning operation was contributing more than half of the BOD5 (mass loading), about three-fourths of the TSS, and almost all the FOG mass loading.
Reducing pH to reduce BOD
Koch Foods first considered acid treatment to drop the pH of the process wastewater prior to the DAF unit. This would provide a more complete breakdown of the oil-water emulsion than the current five-chemical regimen. It was estimated that acidifying the wastewater to pH 2.5 after the EQ basin would increase overall BOD removal of the pretreatment system to about 87%, and produce a final effluent BOD5 concentration of about 330 mg/L. This provided a useful benchmark, but an acid-free treatment would be preferable.
Oxygenation to reduce BOD
Another conventional wastewater treatment method for BOD reduction is oxygenation. While the DAF unit can readily separate BOD solids, it makes only a minor impact on soluble BOD. The most common injection point is after the DAF unit. Moore suggested the aerated EQ tank ahead of the DAF unit as another option.
Koch Foods contacted Messer to design and install a custom BIOX oxygenation system to replace the existing tank aeration. Because air is only 21% oxygen, enrichment with 100% oxygen could potentially provide an effective solution. Estimates indicated that the system also could operate as cost-effectively as acid treatment.
In addition, it would eliminate the need for a new treatment tank, and avoid the associated storage and handling of hazardous chemicals.
In short, BIOX provided a favorable environmental alternative that also was cost-effective.
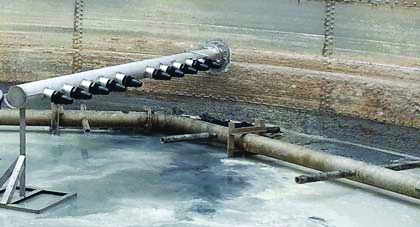
Custom-designed injection header
A dramatic drop in BOD
In the six months leading up to system startup in July 2013, the effluent BOD5 concentration had climbed to an average of more than 900 mg/L with the conventional DAF system. The target for the new oxygenation system was a 50% reduction. After the BIOX installation, effluent BOD5 levels immediately dropped 90%.
The Messer solution for Koch Foods includes a 6,000 gallon liquid oxygen tank with vaporizer and control system. The BIOX control system delivers 100% O2 through a gas sparger that feeds the oxygen enriched water into a custom injection header inside the bottom of the EQ tank. Wastewater in the EQ tank is continuously recirculated back through the sparger. In addition to creating a homogeneous mixture of wastewater, the EQ tank equalizes the flow to the flocculation tubes which are part of the DAF process.
With the BIOX system in place, colloidal and soluble BOD is converted in the EQ tank in one of two ways: 1) Some is oxidized to carbon dioxide and water, which creates energy for the biomass, 2) some is converted into biomass, which is easily skimmed off by the DAF unit.
In the weeks after the BIOX system start-up, effluent BOD5 levels fell on the order of 90%. Even in cold weather, the system operates well within the anticipated reduction target of 50%. Mid-November to mid-February realized an average effluent BOD5 reduction of 63.9% (326 mg/L) compared to the pre-start-up period (903 mg/L).
Learn more about Messer's BOD and COD solutions here.