While cryogenic condensation is used by pharmaceutical manufacturers, it also is suited for solvent and hydrocarbon storage tanks that already use nitrogen for blanketing.
By Rudolf Kuehnel, Bachem Americas, and Neeraj Saxena, Messer Americas
The Switzerland-based Bachem Group specializes in developing and manufacturing peptides and oligonucleotides. As a full-service provider, Bachem offers products for clinical active pharmaceutical ingredient (API) development and commercial applications as well as exclusive custom synthesis.
In its Vista, California, manufacturing facility, Bachem produces — peptides amino acid chains made up of two to fifty substituents, linked by peptide bonds — and related APIs. Nitrogen is used to provide inert atmospheres in the process vessels and to pressurize liquid transfers between operations. It is important to remove the trace organic solvents that are entrained in the nitrogen streams before they are vented to the atmosphere.
Alternative VOC emissions control solutions
To reduce air emissions of these volatile organic compounds (VOC), Bachem investigated various abatement technologies. Thermal oxidation was considered and quickly discarded: it had too large of a footprint and would create ground vibration and excessive noise. In addition, costs were high for the scale of the problem.
A second option, a carbon-based scrubber, was eliminated because it would result in an additional liquid waste stream and increased solid waste in the form of spent carbon.
Cryogenic condensation for VOC abatement
Bachem selected cryogenic condensation. During cryocondensation, cryogenically cold temperatures from liquid nitrogen (LIN) are used to condense and capture VOCs from air or gas. LIN, with a boiling point of -320°F (-196°C), can be used to cool gas streams and condense several different types of VOCs, to allow their capture or recovery.
In addition, the nitrogen used to cool the process gas can be reused to supplement the nitrogen distribution system, which is needed in the manufacturing process.
Cryocondensation provides an effective return on investment for lower flow, high-concentration gas streams. Manufacturers like Bachem, who are already using nitrogen for other purposes, can take advantage of cryocondensation by reusing the evaporated nitrogen. The waste solution allowed Bachem to reinvest in its Vista site.
Reduce VOC emissions with Messer CRYOSOLV™ VEC System
Bachem selected a Messer proprietary CRYOSOLV™ vapor emission control (VEC) system to reduce the atmospheric emission of VOCs. The system uses LIN to recover such VOCs as hydrocarbons, halocarbons, alcohols, and volatile natural compounds. The cryocondensation unit consists of a heat exchanger, temperature and pressure transmitters, automated valves, and a control system.
Vapor emission control system to reduce VOC emissions
The VEC system is suitable for cleaning process gases containing elevated VOC levels and process gas flows less than about 35,000 scf/hr. The condensation point of the substances to be condensed generally should be below -22°F (-30°C). However, the module can be customized for manufacturers with process gases that do not meet standard criteria.
At Bachem’s Vista location, the cryogenic system supplier specified a sub -158°F (-70°C) temperature to attain effective VOC removal.
What are the benefits of a vapor emission control system?
Bachem determined the cryocondensation system was the best available control technology (BACT) and chose the VEC system for several reasons:
- The potential to emit (PTE) from the equipment for each pollutant was less than 10 lb per day.
- The solvent recovery in the process exhaust stream is efficient and effective.
- The LIN refrigerant for cryocondensation is available on-site.
- The system allows Bachem to recycle the gaseous nitrogen created during cryocondensation and redirect it to production processes.
- The cryocondensation module has a small footprint (approximately 10 ft2).
- The process is low maintenance.
- The system does not use chlorofluorocarbons (CFCs).
- The system does not generate secondary emissions (CO2 or NOx) or an additional waste stream.
- It does not require additional waste removal services.
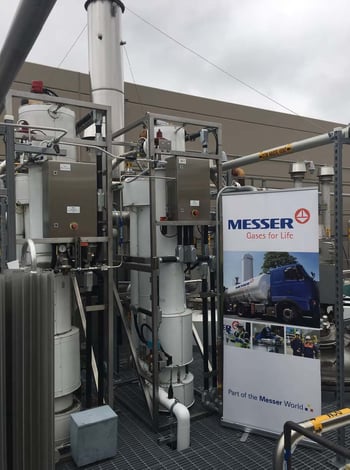
Bachem installed two cryogenic condensation vapor emission control modules at its facility to remove more than 99.8 percent of VOCs from its process stream. One unit operates at a time. The second unit is on standby and takes over when the first goes into defrost mode.
Bachem installed the vapor emission control units downstream of all solvent vent and house vacuum lines. The units condense the VOCs in the exhaust stream: mostly dichloromethane (DCM), dimethylformamide (DMF), isopropanol (IPA) and methanol (MeOH).
The condensed VOCs often are a mixture and are in small volumes that are not separated easily or efficiently for reuse or recycling. Once the collection vessels are full, their contents are trucked to a specialized waste-disposal facility.
In 2017, Bachem installed its first CRYOSOLV™, a model with a 2,000 scfh (50 Nm3 /hr) flow rate. The company added a second module in September 2019. Only one unit is active at any given time. The second unit is on standby and takes over when the running unit goes into defrost mode.
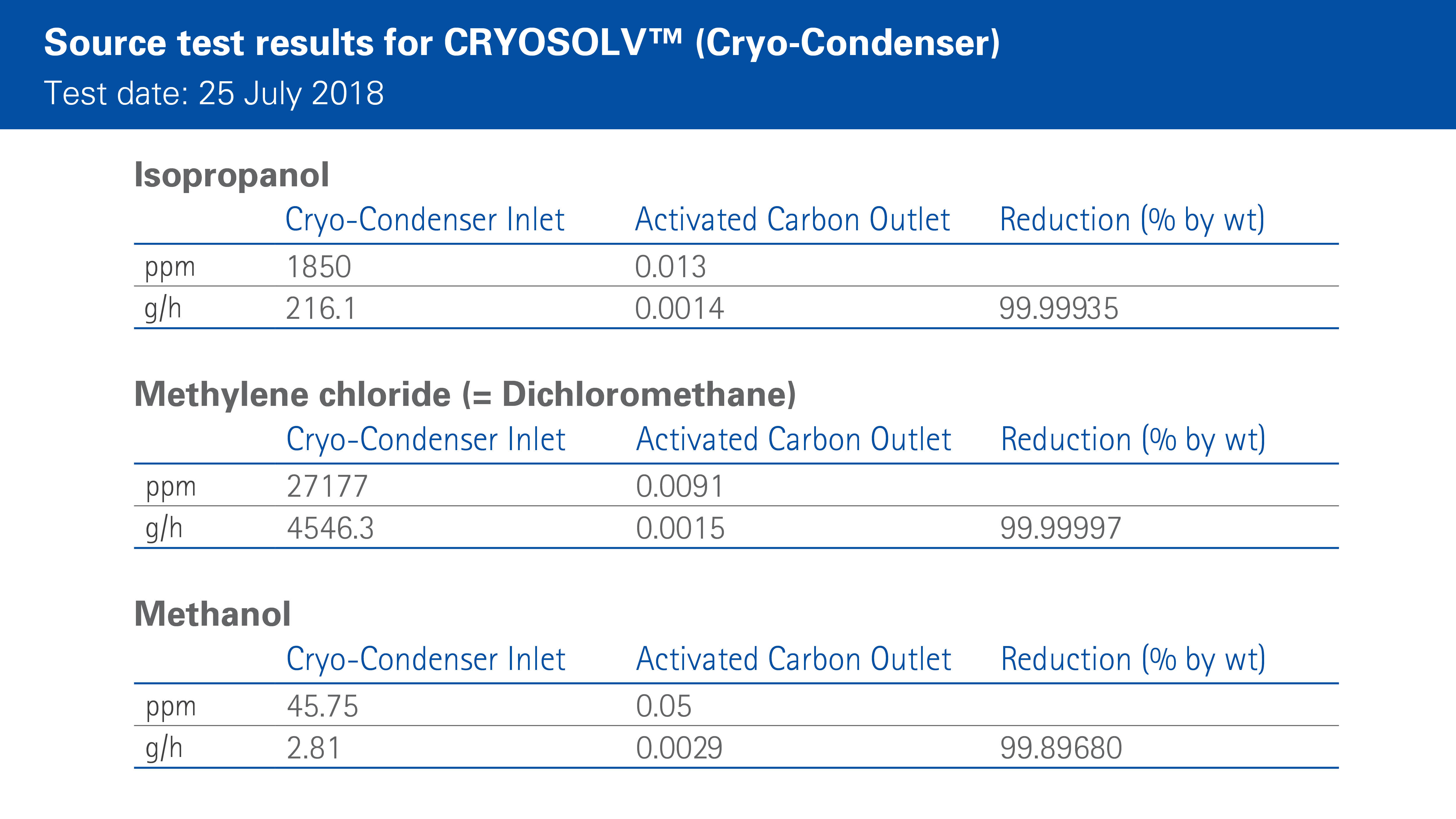
Table 1 shows the results of a source test conducted by the San Diego County Air Pollution Control District. The data shows the concentrations of several VOCs before the emissions stream entered the cryogenic condensation system as well as the values of the exhaust after it exited the activated carbon beds, which are placed in series with the cryogenic condensing unit. The tests show a VOC abatement of 99.896 percent to 99.999 percent by weight.
Cryogenic condensation with the vapor emission control system provided a clean and economical option for Bachem. In contrast, thermal oxidizers — a considered but rejected emissions control technology — can increase NOx emissions, thereby creating another problem while eliminating VOCs from an exhaust stream.
For Bachem and companies like them, that can reuse the nitrogen gas for other processes, the economics of VOC removal improve even more.
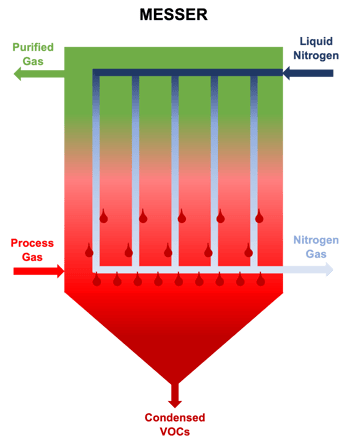
The CRYOSOLV vapor emission control system uses liquid nitrogen to recover VOCs. The cryo-condensation unit consists of the heat exchanger, temperature and pressure transmitters, automated valves and a control system.
Cryogenic condensation for solvent and hydrocarbon recovery
In conclusion, as the pharmaceutical industry continues to grow, good environmental stewardship has become a priority. Air quality monitoring is expected to become more stringent in the coming years.
Cryogenic condensation can be used to ensure that fugitive emissions are captured and not released into the environment. It is expected that the list of acceptable VOC emissions will only become more stringent over time and equipment such as cryogenic condensers can play a role in meeting sustainable manufacturing practices.
While cryogenic condensation is used by pharmaceutical manufacturers such as Bachem, it also is suitable for industrial, chemical, specialty chemical, petrochemical, and biodiesel production.
Potential applications include solvent and hydrocarbon storage tanks that already use nitrogen for blanketing as well as chemical plants or storage terminals that must handle increasing levels of volatile emissions due to expansion.
Learn more about Messer's solvent and monomer recovery systems here.
Rudolf Kuehnel is an engineer/project manager with Bachem Americas Inc., Torrance, California. For more information about Bachem Group, visit bachem.com.
Neeraj Saxena is the director of chemistry, energy and environmental industry with Messer Americas, Bridgewater, New Jersey.